Pros And Cons of Construction 3D Printing: Is It Right for Your Business?
While 3D printing technology itself isn’t necessarily new, the possibilities it offers small businesses across industries certainly are. And these possibilities, of course, extend to the construction industry.
As a business or tech leader of a small construction firm, you might be looking for ways to improve efficiency. Perhaps you’ve been thinking about 3D printing and the ways it could benefit your business. But like with any new technology, it’s important to consider the benefits as well as the costs before diving in.
Glossary of 3D printing terms
If you’re thinking about investing in 3D printing technology or services, you might see a few different terms associated with it in your research. We compiled a few of the most common:
Additive manufacturing and rapid prototyping are different terms used for 3D printing.
Material extrusion is a method of 3D printing where material is deposited through a nozzle. Fused deposition modeling (FDM) is a subtype of this method. Material is wrapped around a spool, heated, and deposited through a nozzle in layers.
Vat polymerization is another method of 3D printing that uses light to harden resin. Stereolithography (SLA) and digital light printing (DLP) are subtypes of this method.
Powder bed fusion (PBF) is another method of 3D printing that uses heat to melt plastic, metal, or ceramic powders to build up layers. Selective laser sintering (SLS) is a subtype of this method. [1]
Not all of these 3D printers can handle the same materials, so it is important to know the types of materials you want to use before making an investment.
How do small construction firms use 3D printing?
Like with any tool, 3D printing has an infinite number of use cases. Depending on your business, you may want to use this technology to create miniature models of projects for clients to review. Creating prototypes of projects may allow you to test designs, mitigate potential challenges, and reduce wasted materials on the job site.
You can also customize building features with intricate designs that are more affordable using 3D printing technology, repair parts for existing buildings, and build entire components of a structure, such as walls, columns, and beams.
Expert insights
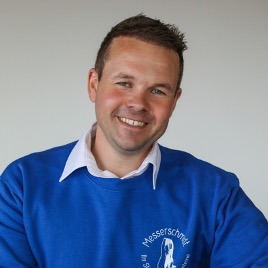
Tobias Messerschmidt [2], founder of Messerschmidt GmbH
Tobias Messerschmidt [2], founder of Messerschmidt 3D GmbH based in Germany, is a trained stonemason who is in the process of transitioning from the gravestone industry to the construction industry, specializing in using 3D printing technology.
“This will change everything,” Messerschmidt says on the company’s website. “It's a revolution in house building.”
Messerschmidt and his team, which comprises tradespeople who are highly skilled in home building and interior construction, take a streamlined approach to 3D printing. For building 3D homes, preliminary work includes traditional construction methods to build the foundation, lay down groundwork, and set up the construction site and printer. It takes about four hours to assemble and calibrate the 3D printer. Then, they print walls, which typically takes two to three days to complete.
“Our current model creates two chambers in the walls,” Messerschmidt said. “One filled with concrete and the other with insulation material, providing both structural integrity and insulation."
After printing, Messerschmidt and his team shift focus to details, such as installing windows. In about three months, the homes they build can be live-in ready, according to their website. [3]
Currently, they use both traditional construction methods and 3D printing to build their homes.
“For some parts, like the roof, and windows, it just does not make sense to use 3D printing today,” Messerschmidt said.
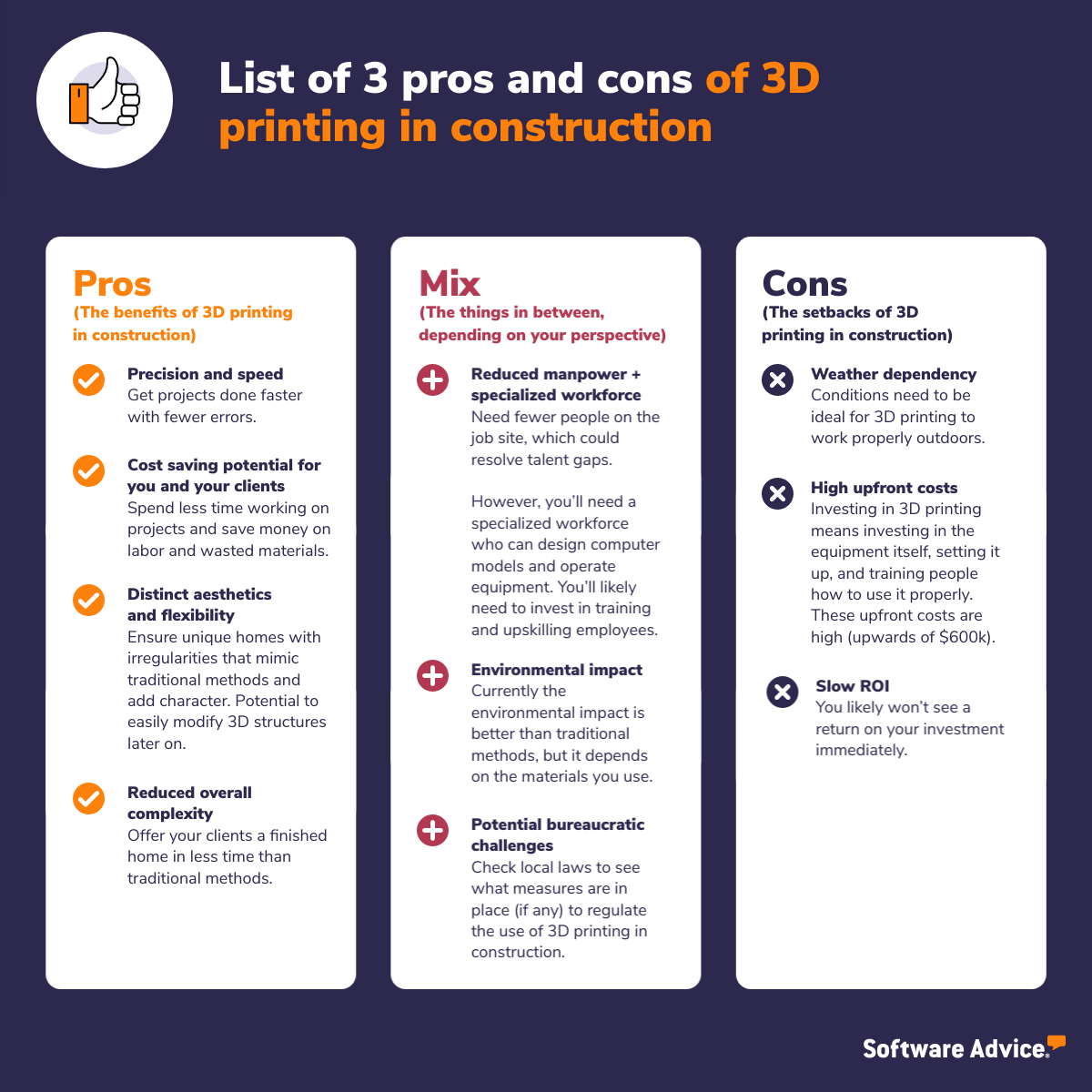
Pros of 3D printing in construction
3D printing in construction offers many pros for small construction businesses and their clients. According to Messerschmidt, 3D printing homes offer clients a less expensive option that doesn’t sacrifice quality, which can help reduce barriers to affordable housing and solve the housing crisis many countries are experiencing. [4]
Pro #1: Precision and speed
Messerschmidt and his team noticed that by using 3D printers, which uses robotics to deposit materials such as concrete, they can offer superior precision over traditional practices.
And they’re faster, significantly reducing building time.
“We estimate a 50% reduction in building time on average,” Messerschmidt said.
Pro #2: Reduced manpower
By 3D printing homes, fewer bodies are required on the job site, which is a pro if your small construction company is having a hard time finding professionals and craftsmen.
For your employees, this could open up opportunities for them to learn the new 3D printing technology and skills.
Pro #3: Cost saving potential for you and your clients
As it stands today, using 3D printing is not possible to use in every stage of the construction process. But Messerschmidt notes that even substituting just one building stage with 3D printing can save your company and clients money.
3D printing’s cost saving potential is linked with its precision and speed that helps cut down on labor costs and materials by both reducing waste generated on the job site and excess purchases.
Pro #4: Distinct aesthetics and flexibility
Even though 3D printing offers precision, Messerschmidt says the resulting homes are not cookie-cutter homes and present their own unique flair.
“Each print carries irregularities reminiscent of natural stone or rubble masonry adding character,” Messerschmidt said. “Every house becomes a unique piece.”
3D printing homes also provides architectural flexibility, making complex designs more feasible and affordable to build, compared to traditional techniques.
It also makes changes and adjustments later on much easier.
“The walls can be moved or installed individually and removed again without much effort,” Messerschmidt says on his website. “If, for example, the children's room is no longer needed, you can use a knife to cut out the wall at the top and bottom and thus remove it within a very short time without causing a lot of dust and dirt.”
Pro #5: Reduced overall complexity
Messerschmidt calls 3D printing in construction a “game changer” in that it reduces the overall complexity of the construction process.
Using this technology to construct walls, for example, simplifies the process by requiring fewer people to be on site, saving resources by reducing material waste, ensuring precision, and getting the job done faster (without sacrificing quality).
Because the walls are built faster using this technology with fewer errors, other aspects of the project don’t get held up for rework or because of bottlenecks in the process. This means contractors, workers, and specialists can come onto the job site faster to do the work 3D printers can’t, such as roofing, windows, electrical, and plumbing.
As a result, Messerschmidt says this technology allows even small construction companies to offer clients full service packages “from empty building grounds to turnkey-home.”
Cons of 3D printing in construction
Although 3D printing in construction presents many benefits, there are also potential issues associated with adopting this technology.
Con #1: Weather dependency
The process of 3D printing outdoors is weather-sensitive, which could limit your construction capacity to specific months and result in longer-than-expected build times.
“A dry and stable climate, ideally between 10-20°C (50-68°F), is necessary during printing,” Messerschmidt said.
At this point in the technology’s development, 3D printing in construction may not be well-suited for every geographic location. Consider your climate—the duration of your rainy season, winters, summers, and humidity—before investing in 3D printing if you plan to use the technology outdoors.
Con #2: Environmental impact
The question of 3D printing in construction’s environmental impact is not straightforward and generally depends on the materials being used to print.
On the one hand, 3D printing can reduce waste and excess materials. Messerschmidt notes that by issuing concrete on-site, they are reducing their carbon footprint and diesel emissions.
However, he also notes that because they currently use cement, which emits carbon dioxide, their carbon footprint is not zero. [5] As a result, Messerschmidt and his team are developing a way to use mud mortar instead.
“This approach would use local soil directly extracted from construction grounds, which would normally be wasted,” Messerschmidt said. Currently, Messerschmidt places 3D printing in construction above traditional masonry in terms of eco-friendliness, but below wooden houses.
Con #3: Specialized workforce
Using 3D printing in construction requires different skills than traditional construction demands. It requires trained personnel to design computer models, operate the equipment safely, and properly maintain the equipment.
Since the technology is still considered new, it might prove challenging to find employees already trained in how to use it. This means you may have to invest in training and upskilling workshops for your team.
Con #4: High initial investment, slow ROI
3D printing in construction requires high upfront costs for the price of the equipment, set up, and the training of employees. Messerschmidt estimates the current investment cost to be around $650k.
These high initial developmental costs mean this technology may not be in every small construction business’s budget (and that’s OK).
“At present, the return on investment isn't substantial due to developmental costs,” Messerschmidt said. “It will be profitable once standardized plug-and-play machines dominate the market.”
Messerschmidt predicts that within the next two to three years, 3D printing will become 30% to 40% more cost-effective than traditional building methods.
Con #5: Bureaucratic challenges
Before investing in 3D printing, check for regulations and legislation surrounding 3D printing in construction. In some cases, these regulations may allow for clear guidelines, while in other places, these regulations may be new and present a barrier to using the technology.
“Planning and approval processes are more tedious [for 3D printing in construction] than traditional means,” Messerschmidt said. “This might be specific to Europe, especially Germany.”
Investing in 3D printing for construction is a personal choice
While 3D printing in construction presents opportunities for small construction businesses, it’s not for everyone. Before you invest in 3D printing, or any new technology such as virtual reality or drones, consider:
The developmental costs and your budget: Can you afford it, knowing it might take a while to see a positive ROI?
How exactly you want to use the technology (e.g., to build entire structures or pieces of structures): Do local laws and regulations allow for this?
Where you live and the climate: Do you have enough days in the year that present the dry, stable, cool weather conditions suitable for 3D printing outdoors?
How much of your current tech stack and process you’d have to change: Is your current construction software or BIM software compatible with 3D printing equipment?
If you decide 3D printing is right for your construction business, be sure to shop around and find the equipment that best fits your needs.
Conversely, if you decide that 3D printing may not be right for your business, keep an eye on how the technology develops over time. It might not be right for your business today, but in a few years, it may become a lower risk, more affordable investment.
Sources
Tobias Messerschmidt, LinkedIn
Augmented reality model of a 3D house designed by Messerschmidt GmbH, Messerschmidt GmbH
“Can 3-D Printing Help Solve the Housing Crisis?” The New Yorker
“Cement industry accounts for about 8% of CO2 emissions. One startup seeks to change that,” CBS News